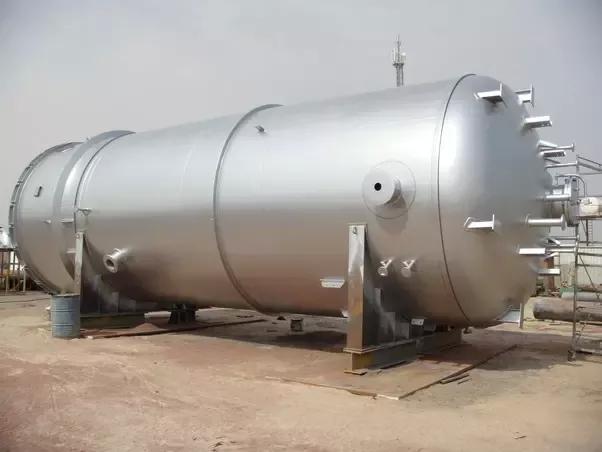
Tapered transitions are common in the industry so they will be familiar to those minimally involved in the design or manufacture of pressure equipment. The form of these transitions is conditioned mainly by the process in which the team is immersed. To conveniently meet the process needs, this conical part can adopt various geometries. The main classification criterion is established by the external shape of the truncated cone, which can be concentric or eccentric, as can be seen below.
It should be remembered that this conical element must be calculated to guarantee that it withstands all the stresses to which it will be subjected throughout its useful life, including manufacturing operations, transportation, lifting of the equipment to its service position, operation, and subsequent dismantling. . Based on the calculation, it can be determined that the thickness of the components involved that had been initially considered is insufficient, so it will have to be reinforced. For this, the most commonly adopted solutions resort to increasing the thickness of the conical or cylindrical element to which it is attached, consider a reinforcing ring, establish radii according to the union between the conical and cylindrical part, or combine several of them.
When it comes to a conical transition that gives continuity in pressure equipment to two cylindrical zones, with the naked eye it can be seen that the union between each cylinder and the cone will cause an abrupt transition in the geometry of the pressure-resistant wall, with its consequent concentration of stresses and imbalance of forces in the joint, unless this always unwanted effect is mitigated. To this end, in the joints between cylindrical and conical elements, a corresponding radius will be used to smooth, as far as possible, the change in geometry and, with it, the stresses present in that area of the equipment. As the numerical value of the radii increases, the existing stresses will decrease.
The effect achieved by these matching radii is, as expected, inversely related to the need, discussed above, to resort to increases in thickness or the addition of reinforcing rings due to the reduction in the stress level. In practice, other secondary variables such as construction possibilities, execution time, or associated economic cost should be taken into account before determining the solution to adopt. We speak of secondary variables since the structural integrity of the pressure equipment will always be of paramount importance over any other considerations, especially in equipment that presents high pressure, extreme temperatures (hot or cold), or suffers variable loads,
As premises when dealing with the calculation of this type of equipment, it should be pointed out that the union between cone and cylinder on the side with the largest diameter, subject to internal pressure, will generally work under compression. Likewise, the cone-cylinder union on the side with the smaller diameter, subjected to internal pressure, will work under tension in most cases. However, if the internal pressure is exchanged for external pressure, the side with the larger diameter will generally be affected by a traction effect while the side with the smaller diameter, by a compression effect. A comment is necessary for relation to the calculation of vertical equipment and its conical transition during transport and subsequent lifting of the same since this vertical equipment is usually transported in a horizontal position and is raised to their service position from the transport position. In no case should this process be overlooked in the calculation, the designer having to ensure the structural integrity of the equipment, especially considering the conical part? Regarding the calculation method, say that, regardless of the design code used, ASME VIII, EN 13445, or AD Merkblatter, the design requirements are similar and, therefore, the results obtained. especially considering the conical part. Regarding the calculation method, say that, regardless of the design code used, ASME VIII, EN 13445, or AD Merkblatter, the design requirements are similar and, therefore, the results obtained. especially considering the conical part. Regarding the calculation method, say that, regardless of the design code used, ASME VIII, EN 13445, or AD Merkblatter, the design requirements are similar and, therefore, the results obtained.
At least the following points must be taken into account when designing a conical transition:
- Cylindrical casing with a smaller diameter: calculation of the thickness required due to the effect of internal and/or external pressures.
- Conical transition: calculation of the thickness required due to the effect of internal and/or external pressures.
- The cylindrical casing of greater diameter: calculation of the thickness required due to the effect of internal and/or external pressures.
- Cone-cylinder joints: calculation of the required reinforcement.
- Radii of agreement (if this solution is adopted): the establishment of requirements to avoid excessive stresses.
From the constructive point of view, it is necessary to take into account that the concentration of stresses, previously exposed, in the joint area between the cone and the adjacent elements may see its detrimental effect increased by a bad fit in the weld between both components. When the conical transition has matching radii, which is widely preferred in the industry, the circumferential welds that will join it to other elements are located outside the area of geometric discontinuities and this arrangement causes a better alignment in the welded joint. It should also be noted that a conical transition with matching radii is a less economical solution. As a solution for the materialization of the radii according, these can be obtained starting from elliptical or spherical head cutouts that have the same thickness and shape required. Often the spokes of the agreement are manufactured in the form of O-rings of the same thickness as the tapered part. Stalwart International One of the best Pressure vessel manufacturers in Vadodara
Also read about:
Positive and Negative Effects of Immigration
How to stay in Mauritius for a couple
10 stuff in Mauritius for couples